Categories
- Shop All (5679)
-
-
- Hi-Vis Chainsaw Safety (14)
- Hi-Vis Coveralls and Overalls (26)
- Hi-Vis Hoodies and Shirts (50)
- Hi-Vis Jackets (37)
- Hi-Vis Pants (21)
- Hi-Vis Rain Wear (45)
- Hi-Vis Vests (53)
- Winter Hi-Vis Bombers and Parkas (22)
- Winter Hi-Vis Coveralls and Overalls (23)
- Winter Hi-Vis Hoodies (4)
- Winter Hi-Vis Pants (4)
- Winter Hi-Vis Vests (6)
-
- Bib Overalls (10)
- Bombers and Parkas (17)
- Coveralls and Overalls (16)
- Disposable Garments (11)
- Flannel and Plaid Work Shirts (21)
- Heated Work Wear (5)
- Hoodies and Sweaters (11)
- Industrial Rainwear (48)
- Pants and Shorts (59)
- Shirts and Sweaters (33)
- Thermal Underwear (43)
- Vests (17)
- Work Jackets (71)
-
-
-
-
- Brooms (0)
- Dust Mops (0)
- Dust Pans and Brushes (0)
- Flow Thru Tools (2)
- Microfiber Mops (0)
- Pool and Tank Tools (2)
- Scrubbers and Scrapers (1)
- Soap and Sanitizer Dispensers (0)
- Sprayers (1)
- Squeegees (1)
- Toilet Brushes and Plungers (1)
- Trash Cans & Bags (8)
- Wet Floor Signs (0)
- Wet Mops and Buckets (4)
-
- Bars and Prying Tools (21)
- Bolt Cutters and Shears (16)
- Chisels and Punches (9)
- Combination Hand Tool Sets (11)
- Extractors (12)
- Files (6)
- Gear Pullers (14)
- Hammers and Mallets (14)
- Hand Saws (22)
- Hex Keys (10)
- Layout and Distance Lasers (1)
- Marking Tools (1)
- Measuring Tools (24)
- Pliers (44)
- Precision Measuring and Testing Tools (24)
- Propane Torches (8)
- Screwdrivers and Nutdrivers (23)
- Sockets (61)
- Tap and Die Sets (4)
- Tool Boxes (27)
- Utility Knives (15)
- VDE Tools (7)
- Wire Cutters and Strippers (14)
- Wrenches (21)
-
- Beveling and Deburring (17)
- Curb and Valve Keys (20)
- Drilling and Tapping (12)
- Extended Impact Sockets (3)
- Flaring and Rerounding (7)
- General Pipe Working Tools (21)
- Guillotine Pipe Cutters (2)
- Hydrostatic Test Pumps (12)
- Internal Pipe Cutters (6)
- Manhole Testing (4)
- PE Peelers (8)
- Pipe Reamers (4)
- Pipe Threading (17)
- Pipe Wrenches (22)
- Plastic Pipe Joint Kits (4)
- Plastic Pipe Saws (5)
- Power Drive (13)
- Quick Release Cutters (15)
- Ratchet Shears (6)
- Ratcheting Wrenches (12)
- Rotary Cutters (3)
- Shut Off Tools (9)
- Soldering Torches (3)
- Vises (7)
-
- Angle Grinders (6)
- Batteries and Chargers (18)
- Bench Grinders (8)
- Circular Saws (3)
- Combo Tool Kits (10)
- Cordless Fans (6)
- Cordless Lighting (15)
- Cut Off Saws (4)
- Drills and Drivers (8)
- Grease Guns (3)
- Impact Drivers (5)
- Jobsite Radios and Speakers (8)
- Lifestyle (7)
- Mitre Saws (2)
- Reciprocating Saws (4)
-
- Angle Grinder Wheels and Brushes (23)
- Bench Grinder Wheels (7)
- Circular Saw Blades (11)
- Drill and Driver Bits (26)
- High Speed Gas Saw Blades (3)
- Holesaws (11)
- Impact Sockets (25)
- Jig Saw Blades (2)
- Oscillating Multi Tool Blades (1)
- Portable Chop Saw Blades (4)
- Power Tool Storage (5)
- Reciprocating Saw Blades (8)
-
-
-
-
- Air Fresheners (2)
- All Purpose Cleaners (19)
- Bowl and Washroom (8)
- Coffee and Breakroom (19)
- Degreasers (3)
- Dishwashing (4)
- Disinfectants and Sanitizers (1)
- Drain Openers (7)
- Hand Cleaners (11)
- Laundry Cleaners (10)
- Paper Products and Wiper Rags (24)
- Scale Removers (4)
- Urinal Pucks and Liquids (5)
- Wet Wipes (4)
-
-
- Ball Valves (14)
- Black and Galvanized Steel Fittings (16)
- Bronze Pipe Fittings and Nipples (13)
- Butterfly Valves (4)
- Check Valves (17)
- Flexible Connectors (4)
- Gate and Globe Valves (6)
- Knife Gate Valves (9)
- Pipe Fitting Accessories (4)
- Schedule 80 PVC Fittings (27)
- Stainless Steel Fittings and Valves (40)
- Victaulic Grooved Fittings (23)
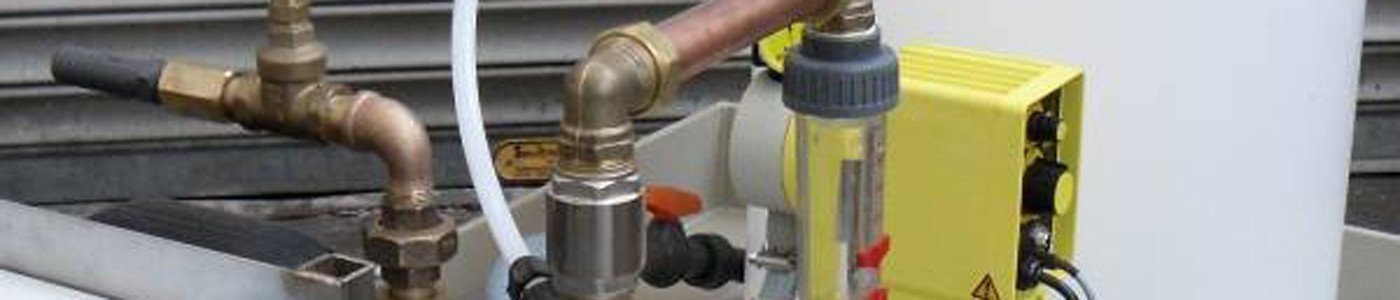
Chemical Metering Pumps
14 products
Showing 1 - 14 of 14 products

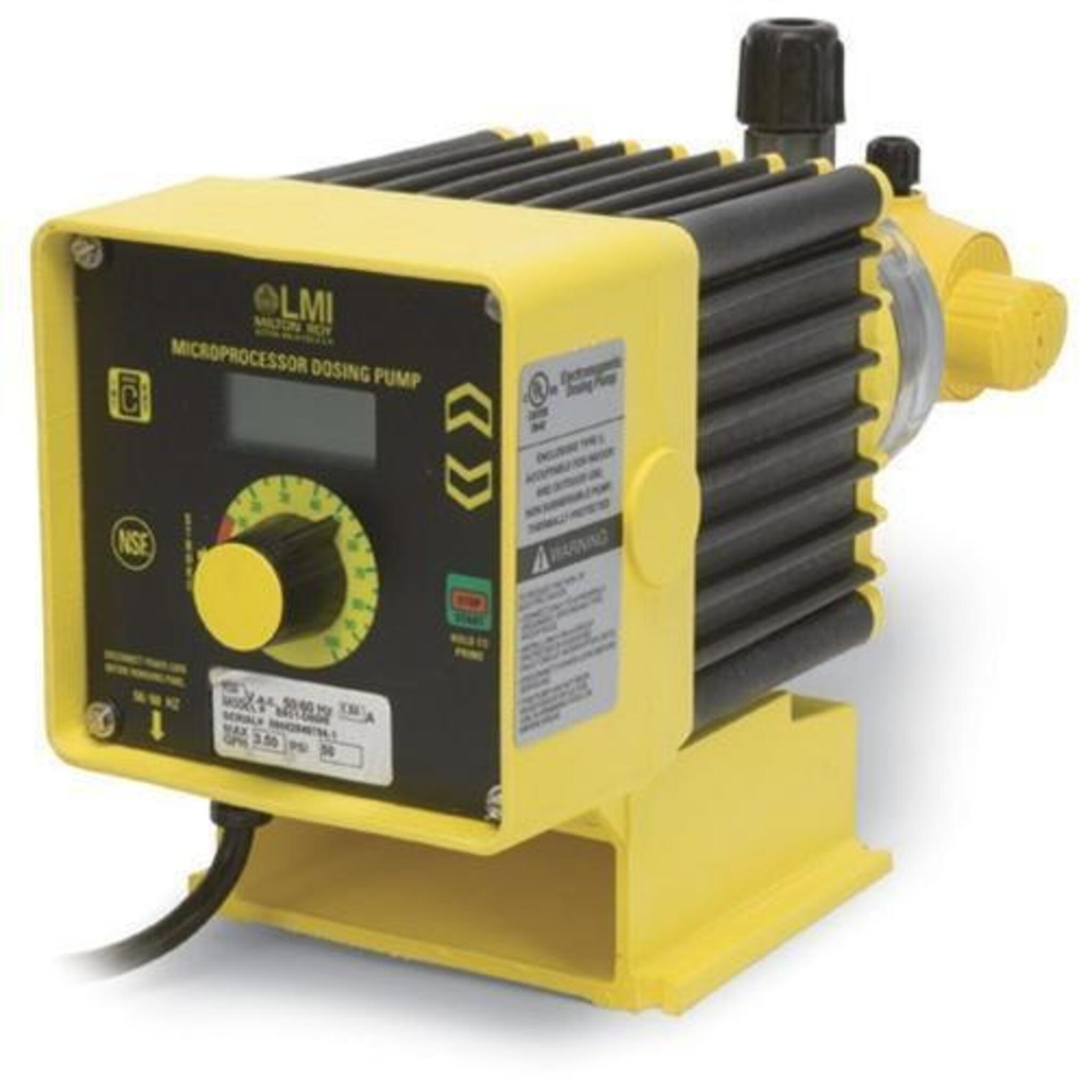
What are Chemical Metering Pumps?
Chemical metering pumps are precision devices used to deliver controlled amounts of chemicals into systems across industries such as water treatment, agriculture, and industrial processing. Designed to handle a variety of chemicals like acids and disinfectants, these pumps operate using either diaphragm or piston mechanisms, driven by a motor to ensure accurate dosing.
Types of Chemical Metering Pumps
-
Piston/Plunger Pumps: Utilize a reciprocating piston to handle high-pressure applications and viscous fluids; commonly used for boiler feed and high-pressure chemical dosing.
-
Diaphragm Pumps: Employ a flexible diaphragm to transfer fluids, making them ideal for corrosive chemicals, slurries, and suspensions. Variants include solenoid-driven, mechanical, and hydraulically balanced types. Hydraulically balanced diaphragm pumps are capable of withstanding high pressures and complying with API 675 standards, making them suitable for critical industrial processes.
-
Peristaltic Pumps: Transfer fluids by compressing flexible tubing with rotating rollers, making them ideal for shear-sensitive or sterile applications; widely used in the food, beverage, and pharmaceutical industries.
Factors to Consider When Selecting a Chemical Metering Pump
-
Flow Rate and Pressure Requirements: It is crucial to select a pump that meets the specific flow rate and operating pressure demands of the application. The pump must be capable of delivering the required chemical dosage accurately and consistently.
-
Chemical Compatibility: Ensuring chemical compatibility is essential to prevent pump damage and maintain efficient operation. Since chemicals vary in properties such as corrosiveness, viscosity, and reactivity, the pump’s construction materials—including the diaphragm, valves, and seals—must be resistant to the chemicals being handled.
-
Accuracy and Precision: For applications requiring precise dosing, such as water treatment or laboratory processes, the pump must deliver consistent and repeatable doses. This ensures the correct chemical concentration is achieved, avoiding issues like overdosing or underdosing.
-
Maintenance and Reliability: Choose pumps that are easy to maintain and have readily available spare parts. Regular maintenance and inspections help ensure reliable performance and extend the pump’s operational lifespan.
Explore Chemical Metering Pumps at Our Canadian Warehouse
-
Pulsafeeder Series C Plus Chemical Metering Pump
-
The Pulsafeeder Series C Plus Chemical Metering Pump offers precise, reliable chemical dosing with dual control dials for independent stroke length and speed adjustment. NSF-61 approved and constructed with durable, chemically resistant materials like Kynar, Teflon, and ceramic, it's ideal for various water treatment applications. Users can choose from three versatile discharge valves to suit specific needs, including options for priming, depressurization, and gas venting—especially useful for chemicals like sodium hypochlorite. Compatible with common treatment chemicals, it operates at 120VAC with 125 strokes per minute and includes all necessary components for installation and maintenance.
-
Pulsafeeder E Plus Automatic Control Metering Pump
-
The Pulsafeeder E Plus Automatic Control Metering Pump is a precision-engineered chemical dosing pump ideal for water treatment applications. It features dual manual dials for adjusting stroke length and speed, and supports 4-20mA remote control for integration into automated systems. NSF-61 certified, it ensures safety and compliance, with durable construction using Kynar (PVDF) and Teflon (TFE) for chemical compatibility. The pump offers various discharge valve options—including quick prime, five-function, and bleed (degas) types—for enhanced versatility. It comes complete with essential components and tubing, making it a reliable and flexible solution for efficient chemical metering.
-
Chem-Tech XP Low Pressure Peristaltic Metering Pump
-
The Chem-Tech XP Low Pressure Peristaltic Metering Pump offers reliable, user-friendly dosing for water treatment applications, featuring self-priming, degassing pump heads ideal for feeding gaseous chemicals like sodium hypochlorite. With adjustable dosing from 5% to 100% via a simple control dial, these pumps deliver precise, low-pressure chemical injection. Standard units include essential components such as tubing, check valves, and a suction strainer, and are CSA and NSF certified for safety and quality.
FAQs
1. Are chemical metering pumps suitable for corrosive chemicals?
Yes, chemical metering pumps are designed to handle a wide range of chemicals, including corrosive substances. However, it is important to select a pump with materials of construction that are compatible with the specific chemical being dosed.
2. Can chemical metering pumps handle high-pressure applications?
Yes, certain types of chemical metering pumps, such as piston metering pumps, are capable of handling high-pressure applications. These pumps are designed to deliver precise dosing at elevated pressures.
3. What maintenance tasks are typically required for chemical metering pumps?
Routine maintenance tasks for chemical metering pumps may include checking for leaks, inspecting and replacing diaphragms or pistons, cleaning valves, lubricating moving parts, and verifying calibration.
4. Can chemical metering pumps be remotely controlled and monitored?
Yes, modern chemical metering pumps often feature digital control interfaces and remote monitoring capabilities. Through internet connectivity, operators can adjust dosing parameters and monitor pump performance from a remote location.
5. What safety precautions should be followed when working with chemical metering pumps?
When working with chemical metering pumps, it is important to wear appropriate personal protective equipment, follow proper chemical handling procedures, and have measures in place to contain and respond to spills or leaks. Additionally, it is crucial to be familiar with the specific safety guidelines outlined in the chemicals' safety data sheets (SDS).